ANÁLISIS CONVERGENCIA ENTRE IT y OT
- QUIMM CHILE
- 6 feb 2020
- 7 Min. de lectura
Hace unos meses atrás, en el contexto de una entrevista a un medio nacional el periodista me preguntó por el grado de automatización que habíamos logrado introducir en la industria chilena, a lo que respondí que, dependiendo de los procesos de cada industria, podíamos hablar con toda seguridad de entre un 60% a un 90%, pero fue la siguiente pregunta la que realmente me sorprendió; “¿y no temen ustedes que, si alcanzan el 100%, ya no tengan más trabajo por hacer?”.
Más allá de explicar que la automatización requiere permanentemente ser calibrada (sensores y actuadores), configurada (controladores), mantenida y actualizada, entre otros factores por obsolescencia tecnológica, todos los nuevos Proyectos, ampliaciones de Plantas e incluso equipos y maquinarias nuevas, se especifican con un alto grado de automatización, lo que implica una tremenda carga de trabajo actual y futura, además, con el advenimiento del Internet Industrial de las Cosas (IIoT) se está abriendo un mundo de nuevas oportunidades, entre las cuales se encuentra el lograr de manera eficiente y eficaz la convergencia entre las tecnologías de información (IT) y las tecnologías de operación (OT), para lograr lo que se conoce como industria IoT, tema que aún no está completamente resuelto, básicamente porque los profesionales de ambas tecnologías parecen venir de “mundos” distintos como lo expresa la siguiente lámina.

Las tecnologías de la información IT son muy conocidas por estar ampliamente difundidas y porque las utilizamos prácticamente todos los días, en la forma de HW y SW (Computadores, Notebooks, Celulares, Smartphones, etc.), en cambio las tecnologías de operación OT, que incluyen a la automatización industrial, son bastante menos conocidas por estar solamente presentes en las industrias y manejadas típicamente por un reducido equipo de profesionales y, culturalmente muy diferentes a los profesionales de IT. A lo anterior, se suma el hecho que la automatización prácticamente no se ve, los procesadores del control automático se alojan dentro de gabinetes especiales y, estos a su vez, se encuentran típicamente dentro de Salas Eléctricas, con acceso muy restringido por razones obvias. Lo que sí podemos ver son algunos elementos sensores y actuadores (válvulas de control por lo general) y, lo más representativo en casi todas las industrias, la “Sala de Control” donde se instalan Consolas de Operación, manejadas por algunos operadores. Sin embargo, ese nombre no refleja lo que realmente sucede en esa Sala, siempre he pensado que debieran llamarse Salas de Supervisión de Operaciones (o de Gestión Operacional) pues allí no reside el Control, de hecho, se podrían apagar todas las Consolas y, con el grado de automatización suficiente, la Planta podría seguir funcionando, sólo que los operadores quedarían sin mirar las variables de los procesos.
Las diferencias culturales entre los profesionales de IT y OT nacen de estudiar ramas diferentes, informática y control automático respectivamente y, luego se acrecientan por conceptos tales como las aplicaciones que manejan. Con la informática tendemos a llenar de aplicaciones de SW, (lo que implica realizar muchas tareas simultáneas) el HW donde se alojan, a veces todo con un solo procesador (lo que frecuentemente produce, por ejemplo, que un PC se “cuelgue”), en cambio a los procesadores de control automático, se les introduce sólo la aplicación de control de un área de procesos y, para mayor seguridad, se configuran de manera redundante los procesadores y sus fuentes de poder. El concepto fundamental es que las aplicaciones de control automático deben ser extremadamente seguras, robustas y confiables, por lo que además se distribuyen en partes del proceso para evitar afectar o llegar a detener una Planta completa.
Otra diferencia cultural radica en el hecho que las tecnologías IT han tratado, tradicionalmente con variables transaccionales (aunque esto está cambiando rápidamente), en cambio las tecnologías OT tratan con variables en “tiempo real”. Un procesador de control tiene tiempos de lectura típicas de 100 ms. o menos, es decir, teóricamente, podrían leer una misma variable 10 veces en un segundo, en la práctica y dependiendo del proceso, muchas variables no cambian tan rápidamente, por lo que no requieren ser leídas con tanta velocidad. De todas maneras, si pensamos en la cantidad de sensores de una Planta, por ejemplo, una Concentradora de Cobre de una gran minera, hablamos de unas 10.000 variables, puede calcularse la enorme cantidad de señales a controlar si los procesadores las leen, típicamente cada un segundo. Para lograr esto, los procesadores de control se distribuyen en la Planta, pero sólo resuelven los lazos de control en tiempo real, comunicando las señales a servidores distintos donde las variables se registran, también en tiempo real y luego se almacenan para análisis y gestión de operaciones y mantenimiento. Las bases de datos que permiten registrar y almacenar por largos períodos de tiempo (hasta 5 años) los datos en tiempo real, utilizando muy eficientemente el espacio de discos y luego desplegar rápidamente todas estas variables en forma tabular o de gráficos, se denominan historiadores de datos o historiadores de procesos.

En algunas industrias se ha popularizado el Departamento TICA, que incluye las Tecnologías de la Información, las Comunicaciones y la Automatización, en un intento por hacer converger ambas tecnologías, sin embargo, en mi vida profesional, todavía veo grandes diferencias culturales y, en muchos casos, conflictos de poder pues todavía se mantienen como feudos separados. Las bases de datos en tiempo real o historiadores mencionados anteriormente, han sido tradicionalmente el punto desde donde los profesionales de IT pueden tomar las variables para generar aplicaciones de valor en niveles superiores, mientras que los profesionales de OT se mantienen a cargo de toda la automatización de las Plantas.
Podríamos decir entonces que los historiadores pasan a ser la interfase entre las tecnologías OT y las de IT, pero falta resolver un tema que, en algunos casos, puede invalidar todo el manejo de las variables a niveles superiores, en especial para efectos de gestión del negocio. Una inmensa cantidad de variables nace de instrumentos sensores en las Plantas industriales, estos sensores deben ser calibrados frecuentemente para representar, lo más fielmente posible cada variable de proceso. Dependiendo del tipo de proceso y las condiciones de operación, muchas veces los instrumentos sensores no se calibran con la frecuencia debida y llegan a presentar errores groseros respecto a la medición real. Lo anterior no es tan significativo a nivel de los Sistemas de Control, pues lo que interesa fundamentalmente es detectar variaciones positivas o negativas y actuar en consecuencia, a través de actuadores para mantener la operación de una Planta dentro de ciertos rangos. En otras palabras, para los Sistemas de Control es más importante detectar las variaciones de una variable que su exactitud respecto al valor real. En cambio, para efectos de una gestión operacional y/o de mantenimiento eficaz, tanto las variaciones como la exactitud pasan a ser muy relevantes. He visto muchas aplicaciones sobre los historiadores que muy pronto pasan al olvido, es decir los usuarios terminan por desechar la aplicación, fundamentalmente por no representar de manera fidedigna las variables reales lo que hace poco creíbles sus resultados.

Es necesario entonces, validar y certificar la información que llega a los historiadores, sobre todo para aquellas variables críticas que pasarán a ser parte de un KPI de gestión.
¿Porque es importante hacer converger ambas tecnologías?, porque la convergencia debiera producir mejoras significativas al negocio. Esto ya fue visualizado hace más de 20 años por una recomendación de las normas ISA (Instrumentación, Sistemas y Automatización, conocida también como Sociedad Internacional de Automatización), a través de la Norma ISA-95 que se enfoca en utilizar las variables operacionales de tiempo real junto con las transaccionales manejadas a nivel de los ERP de las Plantas, lo que permite generar una cantidad significativa de aplicaciones para lograr mejoras a nivel operacional y de mantenimiento de Plantas industriales, estas aplicaciones se conocen como Sistemas MES (Manufacturing Execution Systems).

Hace varios años atrás, tuve la oportunidad de visitar una Planta de cartulinas en el Reino Unido, altamente automatizada donde, por ejemplo, los rollos de cartulina final eran transportados por robots y lo que más me llamó la atención; la “Sala de Control” estaba cerrada y con las luces apagadas pues ¡no había nadie!, me explicaron que sólo la utilizaban muy esporádicamente, sólo cuando había un evento no planeado en alguna parte del proceso, pero quedaba aún lo más interesante, habían implementado un Sistema MES entre el ERP y el Sistema de Control de la Planta. Cada vez que un cliente de Europa entraba a una página para solicitar una cotización de rollos de cartulina, interactuaba “on line” con el ERP, pero al momento de cerrar la Orden y solicitar la fecha de entrega más próxima, el Sistema MES localizaba los “gaps” de las distintas máquinas y situaba la Orden dentro de esos “gaps”, más aún, luego de confirmada la Orden y el plazo de entrega, en un lapso de tiempo no superior a 2 segundos, el Sistema MES optimizaba todas las Ordenes en curso y luego de eso, enviaba las instrucciones al Sistema de Control que comandaba todas y cada una de las máquinas para cumplir con todas las ordenes en curso.
Quienes trabajamos a nivel de OT, acostumbramos a decir que el Sistema de Control es el “cerebro” de una operación industrial, pero en este caso, debemos reconocer que el Sistema MES pasa a ser el “cerebro” del negocio, y es aquí donde adquiere todo el sentido interactuar con profesionales de IT.
En el caso de nuestro país, recuerdo que un jefe de la especialidad de Control Automático de una gran Planta Minera que entró en operaciones el año 1998, planteó el desafío desde un principio de conseguir que los operadores de la Sala de Control, incluso al variar un set-point de un lazo de control, pudieran visualizar, también en tiempo real, si con ese movimiento estaban generando mayor o menor valor al negocio de la compañía. La verdad es que ese desafío no se logró (todavía no lo he visto a ese nivel en ninguna Planta minera), pero estoy convencido de poder alcanzarlo si logramos la convergencia entre IT y OT de manera eficaz, de ahí la relevancia del tema.

La convergencia entre IT y OT se hace aún más necesaria si pensamos en lo que ya está ocurriendo hoy, hablamos de la Cuarta Revolución Industrial o Industria 4.0 que no es otra cosa que la tendencia hacia dónde va la automatización, el intercambio de datos en el marco de las tecnologías de manufactura y desarrollo, marcada por avances tecnológicos impresionantes en robótica, inteligencia artificial, nanotecnología, computación cuántica, biotecnología, computación en la nube e Internet de las Cosas. La Industria 4.0 incluye lo anterior y los representa como sistemas ciberfísicos.
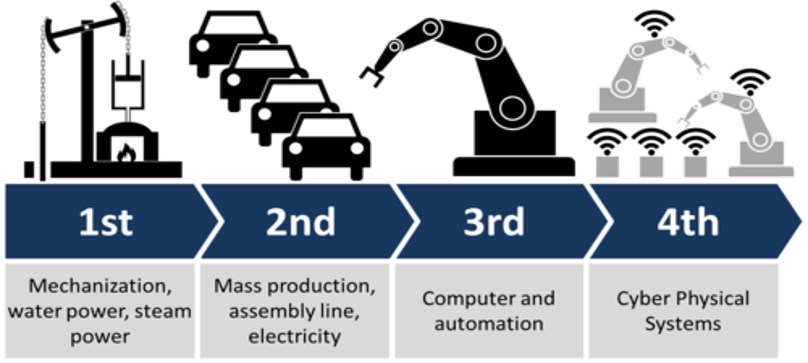
La Industria 4.0 crea lo que se conoce como "fábricas inteligentes". Dentro de la estructura modular de una fábrica inteligente, los sistemas ciberfísicos controlan los procesos físicos, crean una copia virtual del mundo físico y toman decisiones descentralizadas. En el Internet de las cosas, los sistemas ciberfísicos se comunican y cooperan entre sí, al mismo tiempo que lo hacen con los humanos en tiempo real y vía Internet.
En resumen, queda en evidencia que para enfrentar los enormes desafíos que se abren con la Industria 4.0, es absolutamente necesario trabajar en la convergencia OT y IT y, esto pasa por integrar equipos de profesionales de ambas tecnologías. Esto debiera conseguirse a través de talleres de trabajo donde, inicialmente, cada grupo entienda cabalmente los fundamentos de ambas disciplinas para lograr una integración eficaz y que produzca los resultados esperados para cada una de las aplicaciones de valor consideradas. El gran premio, como ya hemos dicho, es lograr mejoras notables al negocio de cada compañía donde se implementen dichas aplicaciones.

Σχόλια